邁入淨零排放時代,扮演建材要角的水泥也要更加低碳。工研院研發「AI低碳無機聚合混凝土技術」,以全循環材料製成「低碳水泥」,並以AI動態智慧配方技術,精準控制水泥品質,相比傳統水泥,可大幅減少90%碳排,榮獲2024全球百大科技研發獎。
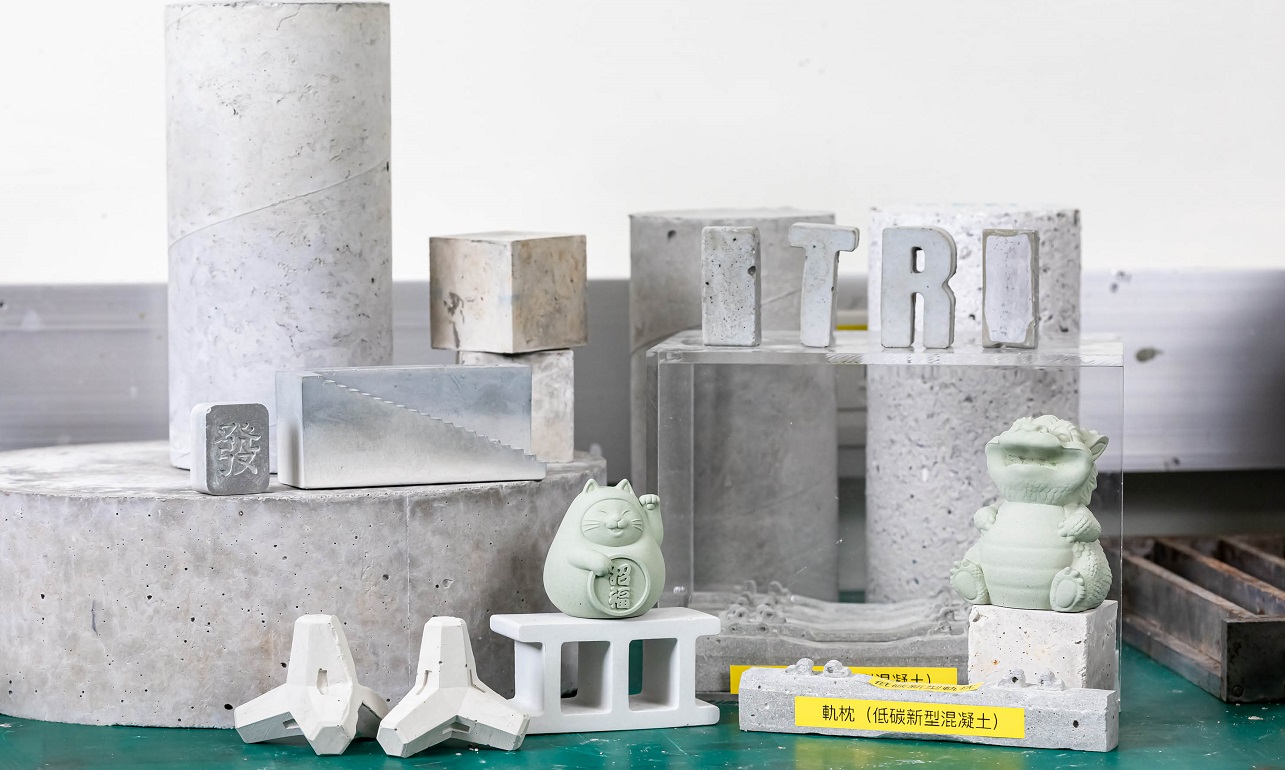
在大樓、橋梁、隧道等建築中,全都少不了水泥的身影,但水泥在生產過程中,卻會排放大量二氧化碳。根據McKinsey數據顯示,全球約有7%碳排來自水泥業,在低碳風潮下,如何降低水泥碳排成了關注焦點。
工研院材料與化工研究所組長邱國創指出,水泥碳排大致可分為兩階段,前段開採和運輸約占總碳排30%,後段經1,500度高溫鍛燒製成熟料水泥則占70%,每生產1公噸的水泥,就產生高達900公斤的二氧化碳,碳排驚人。
在水泥產業之外,臺灣鋼鐵業也有大量爐碴、爐石等副產品需要去化,在循環經濟思維下,團隊以循環材料為主體,以常溫的無機聚合反應技術,取代高溫鍛燒製程,不僅大幅降低水泥碳排,更催生新世代的綠色建材。
化學能取代熱能 大幅減少碳排
所謂的無機聚合反應,是利用鋁矽酸鹽,於常溫鹼性環境下產生膠結反應,使產品具有機械強度。邱國創舉例,就像農民曆中的食物中毒表,某些特定食物個別吃都沒問題,但如果兩個同時吃的話,可能就會引起身體不適。
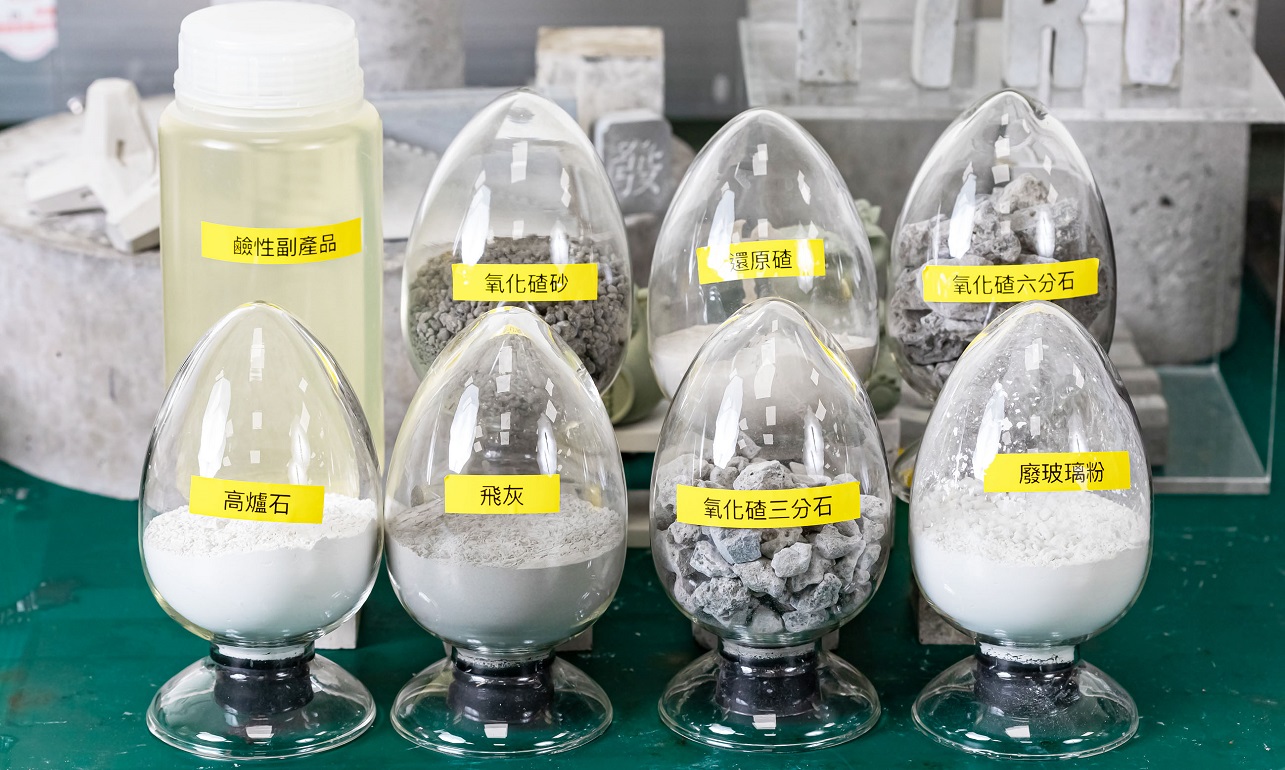
「我們的技術,就是讓不應該碰在一起的物質,全都碰在一起,加入酸鹼誘發化學反應,以化學能取代熱能。」這樣的方式,不僅不用開採全新料源,製作過程也不需要高溫鍛燒,加水一樣也能凝固硬化,相比傳統水泥,可大幅減少高達90%的碳排。
過去團隊投入無機聚合技術已久,但應用在循環材料上卻有全新挑戰,「最大關卡就是料源變異度極大,」傳統的水泥製程配方固定,但循環材的原料複雜,每批的元素組成也大不相同,大幅提高配方排列組合的複雜度,因而影響產出水泥的特性和強度,若光靠人工實驗找出最佳配方解,十分曠日廢時。
不僅原料組成複雜,還要兼顧化學反應的先後順序及反應速度,不是一次把原料全都倒入攪拌,就能完工。邱國創笑說,以前研發工業產品,都希望無機聚合反應愈快愈好,馬上就能變成產品銷售,但水泥不是,從原來的循環材原料開始,到預拌成半成品、半成品輸送,再到現場施工硬化,最後水泥強度的成果,是要等水泥乾掉20天後才能顯現,「這個過程的每一步都要監控,每一個化合反應都要了解。」
AI助攻 找出最佳配方組合
面對複雜的配方計算和化合反應,團隊導入AI智慧平台,只要輸入每批循環材的元素組成資訊,AI便會動態一鍵生成最佳化配方,不僅操作方式簡單,又能確保產品品質,有助後續商業化落地,「水泥最重要的就是信賴度問題,這麼多循環材料回來,都要變成一個穩定產品,技術才有推廣的可能。」
但訓練AI模型又是另一道關卡。循環材料源太多,每隔幾天才能產出一筆實驗資料,短時間內很難累積大量的樣本數據。團隊發展的AI系統,是以小數據生成大數據,先由AI產生初步配方,再經由團隊實驗驗證配方組合是否達到需求,接著產生新數據,再丟回AI系統,不斷訓練之下,AI愈趨精準,目前準確率已經超過8成。
邱國創坦言,若光靠人工計算和實驗,可能3年都做不完;但導入AI以後,團隊大概只花了不到1年的時間進行實驗驗證,就找到最佳化配方,大幅縮短研發時間。不僅強度和傳統水泥一樣,也可依據客戶要求調整配方,生產不同強度和耐磨耗度的水泥。
去化鋼鐵副產品 打造循環經濟
由於建材要求強度,目前臺灣因法規問題,這種新型態的水泥還無法應用在建築結構上,但工研院已和預拌廠業者合作,將新興的低碳水泥用於邊坡、護堤等非結構型的公共工程上。
回首這些年的研發歷程,邱國創有感而發地說,每當在實驗室小量驗證可行後,就要放大到實場驗證階段,團隊用貨車把料源一噸一噸載到現場預拌,親自體會現場操作的問題,「你如果沒有到大太陽下去曬一下,了解工人的辛苦,你不會知道配方應該怎麼改,才能被使用者接受。」
起初老師傅有時會質疑配方,但看到成品愈來愈有模有樣,也逐漸信服,當第一塊水泥產品真正試驗成功時,也是團隊最有成就感的時刻,「工研院很多的研究,不是為了現在,而是瞄準未來需求。」未來在低碳與碳稅議題的雙重壓力下,加上水泥料源愈來愈稀缺,相信低碳水泥的應用空間也會更加寬廣。
(本文由工業技術與資訊授權轉載)