除了在歲修狀態外,半導體產線機台一般都是24小時不停運作,如何維持機台正常運作和產線順暢,影響半導體大廠績效的關鍵,除了台面上的先進製程,更要確保機台不故障不出錯,甚至能在發生非預期停機前故障前,就早一步掌握機台健康資訊。
但一年才歲修一次的半導體機台如何確保其他時間不故障呢?有辦法在不停機的狀態下發現機台的異常嗎?甚至,有沒有可能預先偵測機台的異常並主動警示呢?
根據IBM的研究報告顯示,83%的資訊長認為,設備維護以及總體資產分析最佳化為提升企業競爭力之最主要途徑,導入機台故障預診斷技術效益可以增加20%-25%生產力,工廠產線設備的穩定與正常,是製造業的關鍵競爭力,於是台灣半導體產業找上了工研院的巨量資料分析團隊,希望透過巨量資料分析,預先診斷並排除有可能產生故障的機台。
「半導體機台故障預診斷軟體」這項研究早在四年前就開始啟動,透過蒐集、分析機台資料來監控與評估設備及其零件的健康狀態,及早預測機台需要維修的時間點,減少產線因機台突然故障而必須停頓的風險,原理看似簡單易懂,關鍵就在於AI的應用。
工研院巨量資訊科技中心經理林群惟一語道破關鍵核心:「半導體機台故障預診斷軟體」是一套人工智慧(AI)與機器學習的系統平台,分析機台所產生的製程資料,進行即時監看、預測並以視覺化資料呈現,讓產線管理者可以掌握設備的健康狀態。
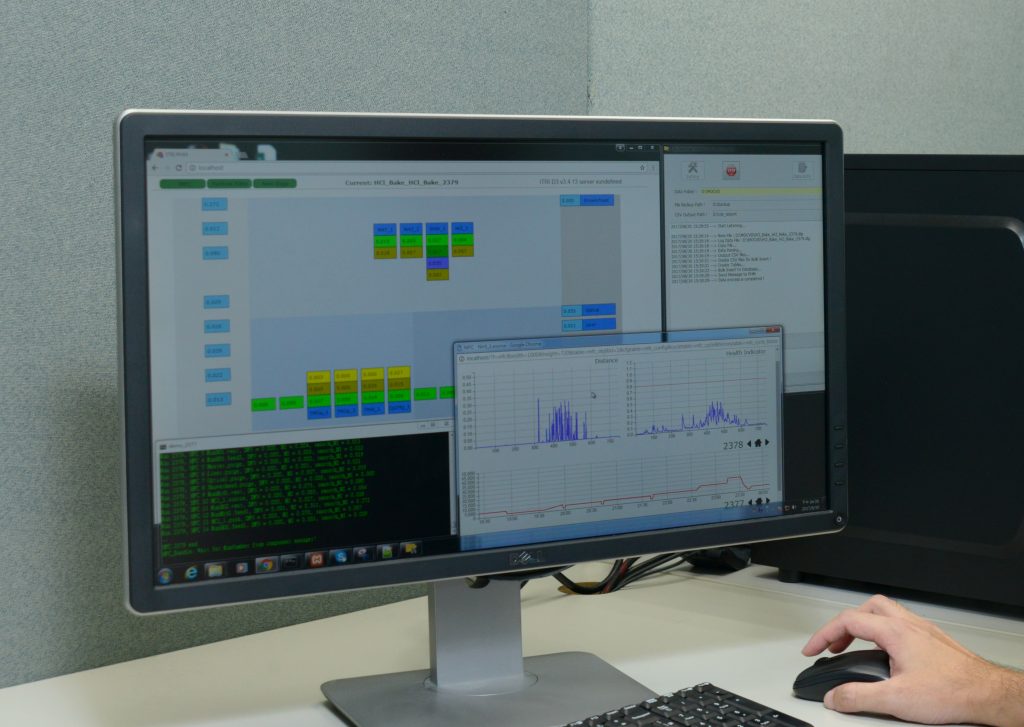
而「半導體機台故障預診斷軟體」獲得光電半導體產業青睞的關鍵技術,在於工研院研發團隊掌握了精準資料蒐集、參數萃取與分析。
關鍵1》蒐集對的資料,從中萃取關鍵參數
由於半導體產線的資料參數,多達400、500種,要從中找到真正影響機台健康的參數,是研發這套系統的第一道關卡,林群惟表示,我們為此整合光、機、電與資訊軟體等領域的研發團隊,經過反覆驗證與測試,順利找出能反映機台設備健康的關鍵參數。
關鍵2》建立整體式學習預測技術
找到能反映機台設備健康的關鍵參數後,接著要建立資料分析模型。研究團隊跳脫過往採用單一「英雄式」的分析演算法,整合數十幾套先進機器學習演算法建立「整體式學習預測分析模型」,提高機台預測分析的準確度。林群惟指出,機台預測分析準確度如果不夠高,一直發出誤警報反而會造成產線工程師的困擾,影響產線生產效率,目前很多智慧製造預測分析技術都有此類問題。而工研院所研發的整體式學習預測分析技術,準確率達到95%以上,減少誤警報的狀況發生。
關鍵3》建立資料分析準則
提高「半導體機台故障預診斷軟體」的準確度還不夠,為將此系統導入更多製造領域的產線,工研院研究團隊進一步建立一套資料分析準則,讓此系統實際導入應用於其他產線時,可以直搗產線生產環節的核心問題,快速建立分析模型。
「半導體機台故障預診斷軟體」藉由預知異常事件即將發生,讓產業提早排除異常,減少突發事件造成的查修時間壓力與風險,提高產線工程師的工作效率,讓工程師專心投入創新研發,為公司創造更多的附加價值,不僅技轉給國內多家光電半導體廠商,同時也入圍2017全球百大科技研發獎。
https://youtu.be/rUSuVOIFgis