AI風潮帶動先進封裝技術發展,工研院打造異質整合封裝的一站式服務,從設計、測試、製造到驗證,更以扇出型封裝光罩共乘服務,加速創新晶片產品開發,強化產學研的研發能量和商轉動力,搶攻未來AI商機。
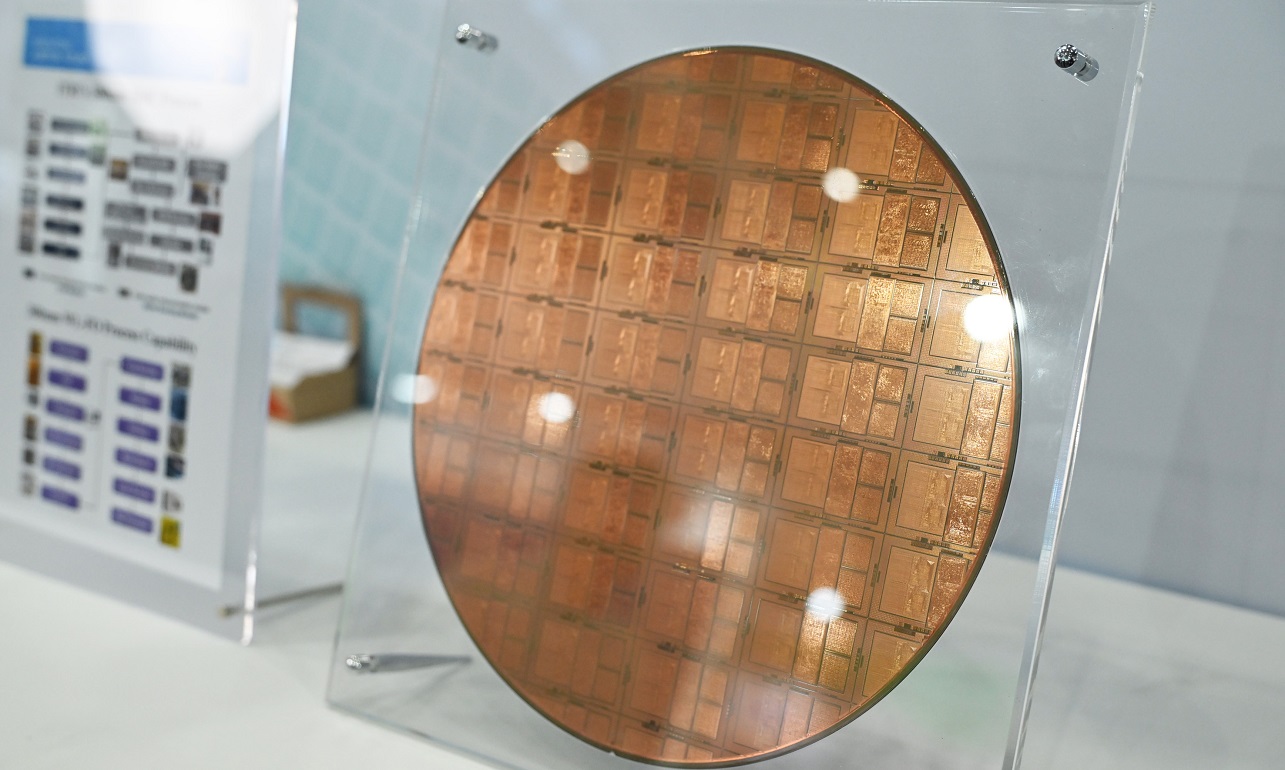
隨著先進半導體製程已達2奈米水準後,電晶體微縮逼近物理極限,為了持續強化晶片性能,滿足AI高效運算需求,半導體技術突破開始看向後段製程,具有高度晶片整合能力的異質整合封裝技術,成了各方搶進焦點。
異質整合封裝簡單來說便是透過先進的封裝技術,讓不同製程、不同功能的晶片,如處理器、記憶體或感測器等整合為一個模組封裝,滿足半導體產業一直以來追求體積縮小、高效能的需求。
瞄準異質整合商機,工研院多年前便投入相關製程研發與材料、設備升級,打造先進封裝製程的專屬實驗室,強化異質整合技術的開發。如今製程產線完備,提供從設計、製造到組裝的異質整合封裝服務,不管是2.5D、3D或扇出型封裝都能滿足,其中最大突破,便是在今年提出的扇出型封裝光罩共乘服務(Shuttle Service)。
新創與學界也能參與先進封裝
工研院電子與光電系統研究所經理張香鈜指出,目前只有台積電、日月光等大廠具有先進封裝能力,但像新創公司或學界,若有先進封裝需求,可能沒有那麼多資源和大廠下訂單。於是工研院打造一個先進封裝的完整製程,之所以稱為「Shuttle」,就是取其接駁共乘的涵義,「讓新創公司和學界用有限的資源,也能搭上這班先進封裝的列車。」
這個共乘服務鎖定現在異質整合最受矚目的扇出型封裝技術,以向外佈線的扇出型方式,提升I/O接點的數量和密度,讓單一封裝能整合更多功能。工研院開出5P6M的固定結構規格,也就是5層絕緣層(Passivation)、6層金屬導線(Metal),可滿足大多新創公司的基本需求。張香鈜比喻,接駁車就是行駛固定路線,如果業者需求與5P6M的結構相符,就能直接上車;如果結構和5P6M不一樣,也可單獨與工研院洽談合作計畫。
光罩共乘的好處是可以大幅降低成本,傳統製作光罩的成本高昂,一個製程的光罩費用可能就高達上百萬。在共乘服務中,工研院將同一個光罩,切割成好幾個區域,再放上不同廠商的路線設計圖,一次曝光顯影,如此一來就能共同分擔光罩成本,就像大家一起共乘接駁車,而不是各自包車。
材料、製程到設備 全力降低翹曲
團隊投入超過3年時間,才打造出這項扇出型封裝共乘服務。張香鈜指出,其中最大挑戰就是翹曲與均勻性難題,因為封裝製程堆疊層數很多,每增加一層,翹曲度也會跟著變大,影響良率。更困難的是,每一層堆疊都有不同問題,不能一概而論,還要針對不同廠商的線路設計進行調整,「這不是一勞永逸的事,無法一次做完以後,就永遠用同樣的參數。」
為此團隊開發一個模擬軟體,可模擬每個材料的翹曲程度,優先選擇翹曲程度低的材料,再搭配熱處理方式降低翹曲;此外選擇設備時,也會考慮翹曲問題,比如黃光設備焦距特別深,不會因為晶片有一點翹曲就無法對焦。
目前這項共乘服務已促成4家業者試產、2家晶片設計公司小量驗證,除了扇出型封裝,未來也希望針對其他如2.5D、3D等先進封裝技術,提供共乘服務,滿足產業更多先進封裝的製程需求。
低溫混合鍵結等先進技術 促產業百花齊放
工研院的先進封裝實驗室具備多項重要技術,現階段技術水準可達到2微米細線寬、線距,提升訊號傳輸和頻寬;此外還包含3D直通矽穿孔(TSV)、微型凸塊(Micro Bump)、混合鍵結(Hybrid Bonding)等技術,幫助廠商開發先進封裝解決方案。
其中,工研院實現了在180℃相對低溫完成Hybrid Bonding接合的突破,同時創下最低電阻值的紀錄。過去主流封裝方式透過錫球凸塊連接晶片,Hybrid Bonding則是透過銅與氧化物鍵結,使晶片金屬墊直接接觸並提升連接密度,達到更快傳輸速度與降低耗能。
張香鈜指出,傳統銅接合需在3、400℃的高溫並超過20分鐘退火下進行,但高溫易引發晶片翹曲以及記憶體元件特性變化,對高階晶片製程不利。為解決此問題,工研院選用奈米細晶銅替代傳統的銅材料,加快加熱擴散速度,並結合晶種層沉積、電鍍調控等技術,成功在180℃以下實現Hybrid Bonding。
張香鈜觀察,近年AI浪潮下,對算力與資料傳輸速度的需求不斷提升,進而推動晶片堆疊與異質整合封裝技術的發展。工研院的異質整合封裝技術與光罩共乘服務平台正是瞄準此一趨勢,盼能促成臺灣半導體技術創新百花齊放,在AI時代拔得頭籌。
(本文由工業技術與資訊授權轉載)