全球半導體產業鏈,從晶片設計到生產製造,臺灣都屬於佼佼者,然而,隨著AI時代來臨,晶片設計與製程愈來愈複雜,使得檢測技術面臨前所未有的挑戰。工研院研發「陣列3D檢測技術」,為半導體檢測帶來新突破,大幅提升檢測速度與效率。
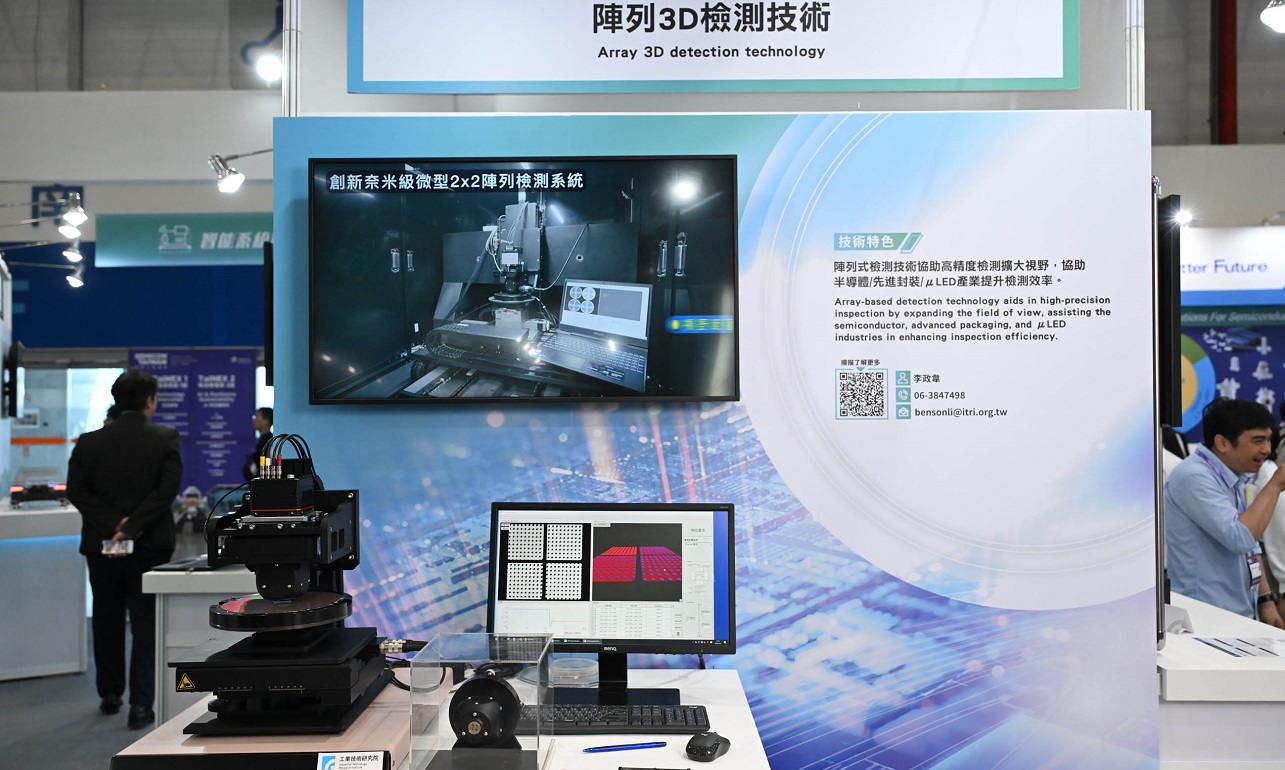
半導體製程動輒數百道工序,任何一個環節出現瑕疵都可能影響產品良率,因此,檢測環節扮演重要角色,晶圓表面或電路結構中的潛在異常、污染、刮傷或短路等,這些結構性缺陷可能嚴重影響晶片的性能,為了確保產品品質,半導體廠必須嚴格監控每道製程。
「傳統檢測技術運用高倍數單鏡頭,以2D方式檢測,雖然能夠提供高精度的檢測結果,但隨著晶片面積增大和元件縮小,且朝著3D堆疊方向發展,檢測技術勢必得跟上,如何在更大的範圍內進行精密檢測還能維持高效率及精準度,成為檢測技術的重要課題。」工研院智慧感測與系統科技中心研發副理甘凱翔說明,為協助半導體封測製造服務業技術升級,工研院3年前開始投入研究,探索如何提升檢測效率,「陣列3D檢測技術」於焉誕生。
從單眼到複眼提升檢測效率
「比起以前的2D單鏡頭檢測,陣列3D檢測技術有4顆鏡頭、以2×2的陣列配置,相當於4顆眼睛同時進行多鏡頭自動化顯微校準,檢測速度自然能提升4倍,」甘凱翔強調,這項技術的突破,讓檢測從依賴單鏡頭放大的方式,轉變為多鏡頭同步工作,達到倍數增長的效果。這種「複眼」的概念,使得檢測技術可以同時覆蓋更大範圍,並且保持高精度,滿足現代半導體製造過程中對大面積、高精度檢測的需求。
「相比之下,傳統2D檢測只能針對平面進行檢測,陣列3D檢測更可建立完整的3D資訊,不僅改變檢測流程,還大幅提升檢測的速度與效率,」甘凱翔解釋3D檢測的優勢所在。
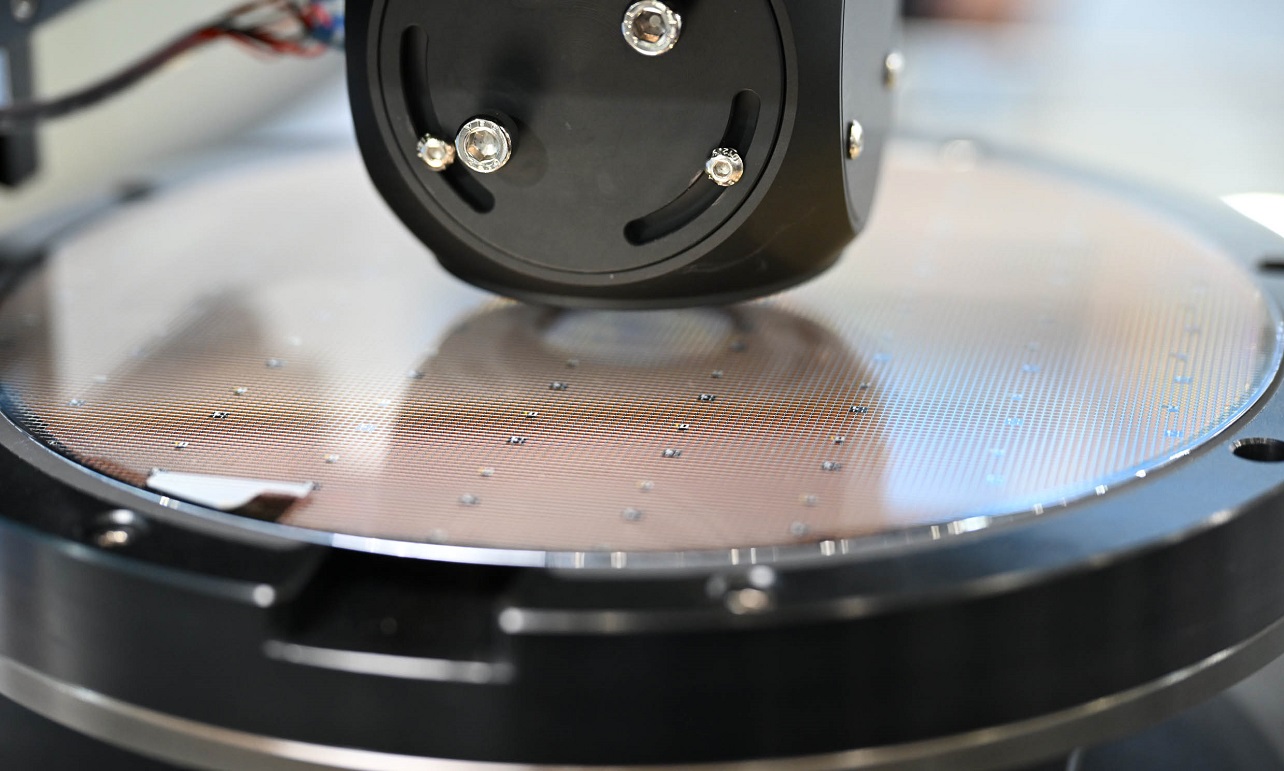
多項專利突破技術瓶頸
從1顆眼睛變成4顆,需突破的挑戰很多。由於3D檢測技術從微米級一口氣提升到奈米級別,其核心元件即「壓電元件」(PZT),負責驅動感測頭,但壓電元件承重能力上限為5公斤,無法乘載4顆鏡頭的重量。為解決問題,團隊對元件進行微縮,最終將4顆鏡頭的總重量成功控制在2.5公斤內,瘦身成功後還要確保每顆鏡頭的精度與傳統單鏡頭相當,讓檢測系統不僅能夠快速工作,還可保證檢測結果的精確性。
甘凱翔表示,「更關鍵的挑戰是鏡頭校準,當多顆鏡頭無法準確對齊時,檢測就會不同步,一旦出現『眼花撩亂』、4顆鏡頭互相干擾的情況,反而會拖緩檢測速度。」為此,團隊精進鏡片MEMS異質複合鍍膜技術,以杜絕多鏡頭產生的鬼影狀態,甚至連光源、光路都重新設計過,打造出半自動化的共面度校正平台,針對共面度誤差的測量和調整,申請多項專利技術。
彎道超車增強臺灣競爭優勢
甘凱翔指出,雖說臺灣在半導體領域位居領先地位,但這多是指製造技術,實則檢測技術長期依賴國外技術與設備,如KLA、KEYENCE等歐美日等國企業,皆為全球檢測技術的領航者。然而,隨著國內研發實力的提升,檢測技術也逐步擺脫對國外技術的依賴。陣列3D檢測技術的問世可說是「彎道超車」,即便是國外知名半導體檢測大廠,其多鏡頭功能目前仍停留在微米級別,工研院的技術已經能做到奈米級多鏡頭檢測,為臺灣在半導體檢測技術領域創造更大的話語權。
「為了讓技術更具說服力,已完成美國國家標準技術研究所(NIST)的設備標準件量測,誤差能控制在10奈米以內,技術已完美達標。」回想這段研發時光,團隊還聯合廠商與民間企業共同參與。目前陣列3D檢測技術已滿足4顆鏡頭的運作,未來只要突破算力瓶頸,相信增加到8顆鏡頭也不是問題。
檢測技術掌握在國內廠商手上,最大好處是,未來臺灣半導體製造商遇到問題時,技術團隊可迅速反應並及時提供解決方案,這種快速應變能力是跨國企業難以實現的;技術團隊更能與半導體產業緊密合作,提供客製化服務,使臺灣在檢測技術的開發上能夠更加靈活應對市場需求,讓臺灣半導體產業如虎添翼,朝設計、研發、製造與檢測一條龍邁進,在全球半導體領域穩穩立足優勝者地位。
(本文由工業技術與資訊授權轉載)