氫用作工業原料已很普遍,多數使用天然氣搭配水蒸氣重組法,成本低但碳排高。為達2050淨零排放,低碳製氫逐漸興起,國際能源署(IEA)《2024年全球氫能回顧報告》指出,若要符合2050年淨零排放情境(NZE Scenario)的目標,低碳氫的需求需達到6,500萬噸/年,顯見未來低碳氫的產製與相關產業鏈,可望大幅成長,極具市場潛力。
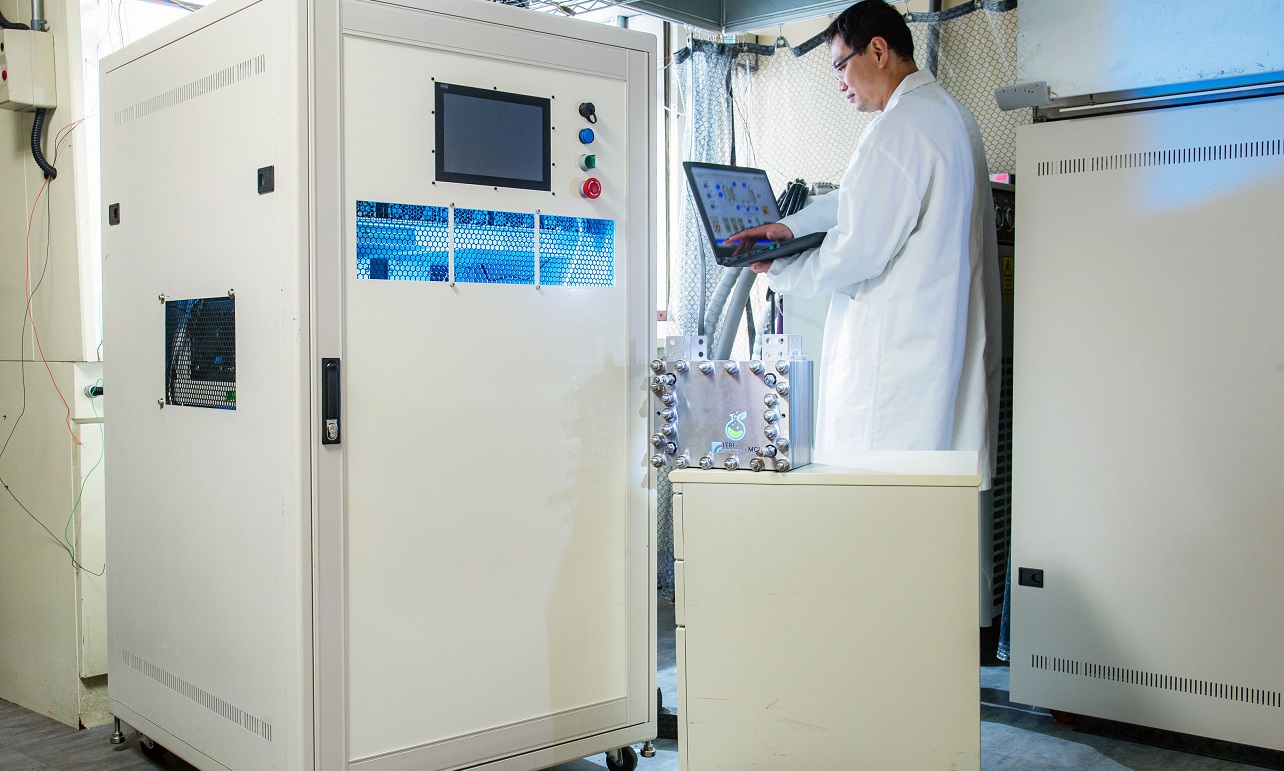
根據國際能源署(IEA)《2024年全球氫能回顧報告》(Global Hydrogen Review 2024),2023年全球氫氣生產量超過9,700萬噸,超過80%的氫氣來自化石原料製造,主要技術包括天然氣重組和煤炭氣化;而煉油及其他石化產業等工業副產氫供應量則占15%。
相比之下,低碳氫的占比在過去2年均低於1%,包括以化石燃料搭配碳捕捉、利用及封存技術(CCUS)生產的藍氫,以及再生能源電解水產生的綠氫,年產量不足100萬噸。對此,工研院產業科技國際策略發展所產業分析師黃霈瑜認為,現階段產氫雖以化石原料為主,未來低碳氫才是主流。
「再生能源電解水產氫有低碳優勢,因其製氫生命週期所產生的碳排放量,遠低於化石料源製氫或一般市電電網製氫,因此在全球淨零趨勢下,勢必將成為主要發展國家及開發業者的推動主力。」黃霈瑜說。其中,電解水產氫系統是綠氫的關鍵設備,由於受惠政策驅力,整體裝置量與供應鏈皆已邁入快速成長階段,而「電解系統」相關供應鏈也已積極投入生產布局,預期至2030年,電解水產氫裝置量合計占比將接近8成。
鹼性膜電解水產氫技術 高效低成本
電解水產氫發展可追溯至18世紀末期,直至1902年,全球已有400套電解系統用於工業應用。工研院材料與化工研究所組長蔡麗端表示,電解水產氫技術是一種透過水和電產生氫氣的電化學反應,目前全球主要的電解水產氫技術約有4種,包含鹼性電解水產氫(AEL)、質子交換膜電解水產氫(PEMEL)、固態氧化物電解水產氫(SOEC)與鹼性膜電解水產氫(AEMEL),其中鹼性膜電解水產氫技術,因具低成本、環保、且不需貴金屬觸媒,被認為是值得發展的新興電解水產氫技術。
工研院自2017年起,即投入鹼性膜電解水產氫技術,可透過整合整合綠電與電解水產氫,產出綠氫,該技術涵蓋關鍵低成本鎳基觸媒材料,成本較貴金屬觸媒節省90%;高效率膜電極組設計,電解效率超過80%;以及耐壓型電堆組裝設計、低耗能系統整合技術等,全為工研院自主研發,適用於鋼鐵、石化、電力、半導體產業。
工業餘氫 現階段便利經濟的氫來源
以再生能源電解生產之綠氫成本偏高,工業副產氫若能夠重複利用,是更便利、經濟的來源。工研院綠能與環境研究所組長張文昇表示,氫氣在工業上的應用相當普遍,包括石化、面板、電子、半導體產業等,都是製程中會用到或製程衍生的化學物質。
「工業餘氫對環境不會造成污染,過去業者大多經處理後排放,或石化業者會用作為熱電共生的燃料,在淨零排放目標下,工研院期待透過純化技術,將工業餘氫回收再利用,」張文昇說明,要將餘氫回收並不容易,由於現行的工業產氫大多來自天然氣以及化石燃料,產製過程中,氫氣純度僅不到70%,張文昇分析:「若要用於燃料電池發電,一般須將氫氣純度純化到99.9%以上,才能進到後端的應用。」
工研院與工程設備大廠帆宣、氫能源商亞氫動力攜手籌組「氫能發電團隊」,投入製程餘氫回收發電技術,結合工研院氫氣回收控制技術、帆宣科技發電系統整合技術以及亞氫動力的燃料電池,以氫氣發電滿足國內工業減碳需求;同時,餘氫發電技術,已技術移轉氫豐綠能科技,進行產業化推動,搶攻臺灣低碳氫能應用商機。
高效濾氫純化模組 提升氫純度7N至9N
餘氫再利用,純化技術是關鍵。工研院的「高效濾氫純化模組」,透過篩分隔離與質傳過濾雙機制,將半導體、石化等產業製程產生低純度(約50%)的餘氫,進行純化回收後再放進入產線循環利用,可提升純度到7N至9N。「該純化模組採用低成本的陶瓷金屬材料,部分取代昂貴鈀金屬,提升其成本優勢,體積也僅現有技術的一半,」張文昇說。
擁有超過20年燃料電池開發經驗的亞氫動力,採用工研院「高效濾氫純化」技術,將回收餘氫純化再接入燃料電池發電,具有低碳排、低噪音且發電效率高的優勢。亞氫動力總經理蕭逢祥表示,與工研院的合作,主要由工研院分析餘氫成分,提供純化技術,亞氫則在安全性上著墨,提供防爆設計、安全隔離技術,確保燃料電池的安全穩定。
「目前全臺灣純氫發電機不到1MW,如果能充分運用工業餘氫,估計可以發出100MW的電。」蕭逢祥認為,純氫與餘氫成本差距10倍之多,是最經濟的氫來源,「我相信,氫能發電的市場正在從原本的利基市場,走向成熟。」
(本文由工業技術與資訊授權轉載)