隨著全球對氣候變遷和環境永續的關注日益增強,創新的低碳製造技術不僅能夠協助產業減少碳排放量,降低對環境的影響,更能提升生產效率,有效利用資源,進而節省能源成本。工研院深入了解產業需求和挑戰,開發出多項低碳製造解決方案,為實現綠色、低碳的未來努力。
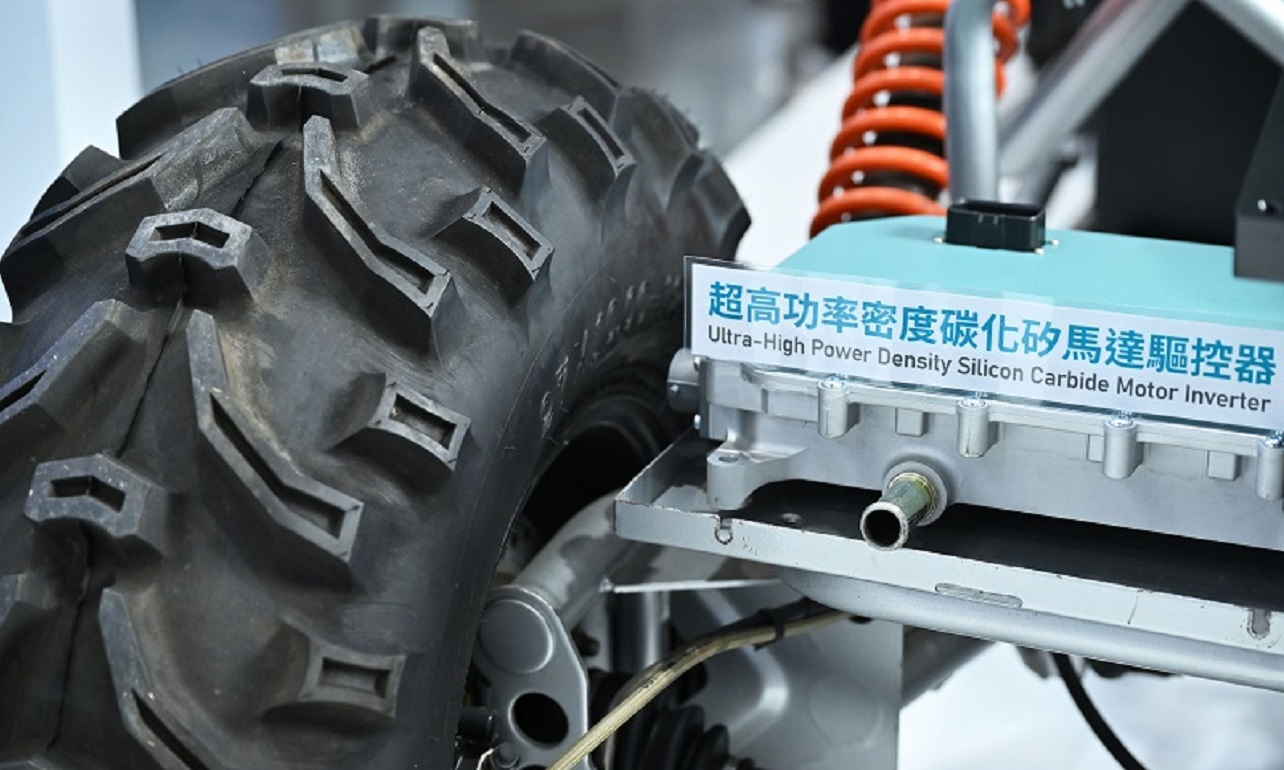
臺灣是出口導向國家,面對國際各國陸續制定碳稅、碳排限制等壓力,產業必須採取積極措施以降低碳排放。為此,垂直分析、檢視製程中的碳排放量成為關鍵,除了採用綠色生產方式和節能設備來減少能源消耗和碳排放,同時也需著重研發創新的減碳技術,以尋求更加低碳製造的方法來達到碳中和目標。
超高功率密度碳化矽馬達驅控器 小體積大電力
因應全球淨零排放趨勢,在交通運輸減碳上,全球已有超過20個國家訂定車輛電動化或燃油車禁售令,帶動電動車產業蓬勃發展。車輛電動化之後,電池提供直流電(DC),但馬達運轉卻靠交流電(AC),要讓馬達動起來,中間要有橋梁,把DC轉AC,這個橋梁就是馬達驅控器。
為提升電動車續航力,須提高動力驅動效率,一直是各家車廠努力研發的方向。工研院開發「超高功率密度碳化矽馬達驅控器」,具備高切頻、小體積、高效率、耐熱佳等特性,可應用於高壓大功率之電動貨車或巴士,為動力驅控器國產自主開發方案。
雖然碳化矽有先天的材料優勢,但仍有許多周邊設計需要互相搭配。首先,高切換頻率雖可減少切換損失、提升馬達控制效率,但也會衍生電磁干擾問題,因而要採取高頻抗雜訊的驅動電路設計;其次,因為更耐熱,散熱系統也要做更嚴謹的設計,工研院透過開發主動溫度估測補償技術,確保模組溫度。
透過整體的模組結構設計,碳化矽馬達驅控器的功率密度也有提升。一般馬達驅控器的功率密度大約在20kW/L,工研院研發的碳化矽馬達驅控器卻擁有60kW/L的高功率密度,以及大於98%的高效率表現,符合美國能源部對電力驅控系統2025年須提高至100kW/L的階段性目標。目前車用馬達驅動器已技轉給東元電機,根據東元電機預估,至2030年市占約8,000輛大巴士,每輛每公里的碳排減量約2公斤,每年以4萬公里計算,可減碳約64萬噸。
混合電力整車控制器 電動車新頭腦
若電動車的動力系統是心臟,那麼,整車控制技術就如同電動車的大腦。放眼全球,電動車是最具前瞻性的重點產業之一,各國對汽車排放法規的要求愈來愈嚴格,同時隨著整車用電設備的增加和複雜化,市場上出現了愈來愈多的混合動力車型,無論鋰電池或是未來前景可期的氫燃料電池,如何巧妙轉換不同性質的電力來源,混合電力控制新技術正是讓電動車更聰明、有效率的神器。
由工研院研發的「混合電力整車控制器」,可謂是國產的電動車超級大腦。該技術為模型化基礎(Model-Based )設計,並依據ISO 26262的設計規範,可自動生成程式碼,加上以CAN進行軟體執行碼編寫及調校,且硬體採用ASIL D等級的微控制晶片及電源管理晶片,使用在電動車鋰電池與氫燃料電池的混合電力控制上,就能使控制馬達化成電動車前進的動力。
該技術是國內第一個專為氫能車打造的混合電力控制器,提供整車控制器與車用軟韌體方案,可望加速氫能載具布局。其中,電動車整車控制器已導入中興巴士集團、鴻華先進、成運、創奕及華德等多家電動巴士領導廠商,累積豐富的實車道路驗證經驗,更於2022年促成新創公司「科飛數位」成立,預期目前所開發的混合電力控制器未來在氫能運行載具發展產業推動,亦將扮演關鍵角色。
視覺擬真出鋼雙生系統 確模擬煉鋼製程
被視為耗能大戶的煉鋼廠,面對淨零排放的考驗,壓力更大,因其煉鋼製程非常複雜,需根據客戶訂單調整鋼液的成分和溫度,以確保產品符合品質標準,操作員投入合金也會採取較保守策略,以避免產品不合格而被退貨,但如此一來會增加投料成本。中鋼在2023年成立「數位轉型推動小組」,將一貫化煉鋼製程全面導入智慧製造,開發各種智能化方案以提升生產效益,並委託工研院攜手研發「煉鋼出鋼製程視覺擬真雙生系統」提升製程智慧化,減少人為開發,提供更準確的模擬結果,協助決策。
出鋼製程數位雙生環境是一個虛實同步的模擬系統,有別於過往傳統製程需耗費大量人力物力,經驗傳承不易,製程失敗所增加的潛在成本與環境汙染較高,且一般的數位雙生多為純數字處理,此模擬系統可藉由系統內「製程過程與操控之研究分析」、「回顧並檢討過往製程控制」、「即時製程虛實同步觀看」及「分析即時製程狀態並提供操控建議」等4種不同模式,來幫助且優化實際出鋼製程,達到擬真視覺化成像。
該系統將傳統的出鋼製程推向數位化,協助煉鋼廠因應淨零排放的國際趨勢,降低過往轉爐製程所耗費的成本,以最快速有效的方式避免不必要的汙染,同時製程數值化,更有利於經驗傳承。
(本文由工業技術與資訊授權轉載)